Features of High Frequency Induction Furance
Rugged and Long Life Furnace Body Construction
Realizing durable and long life furnace body construction by tightly clamping both circumference and vertical direction.
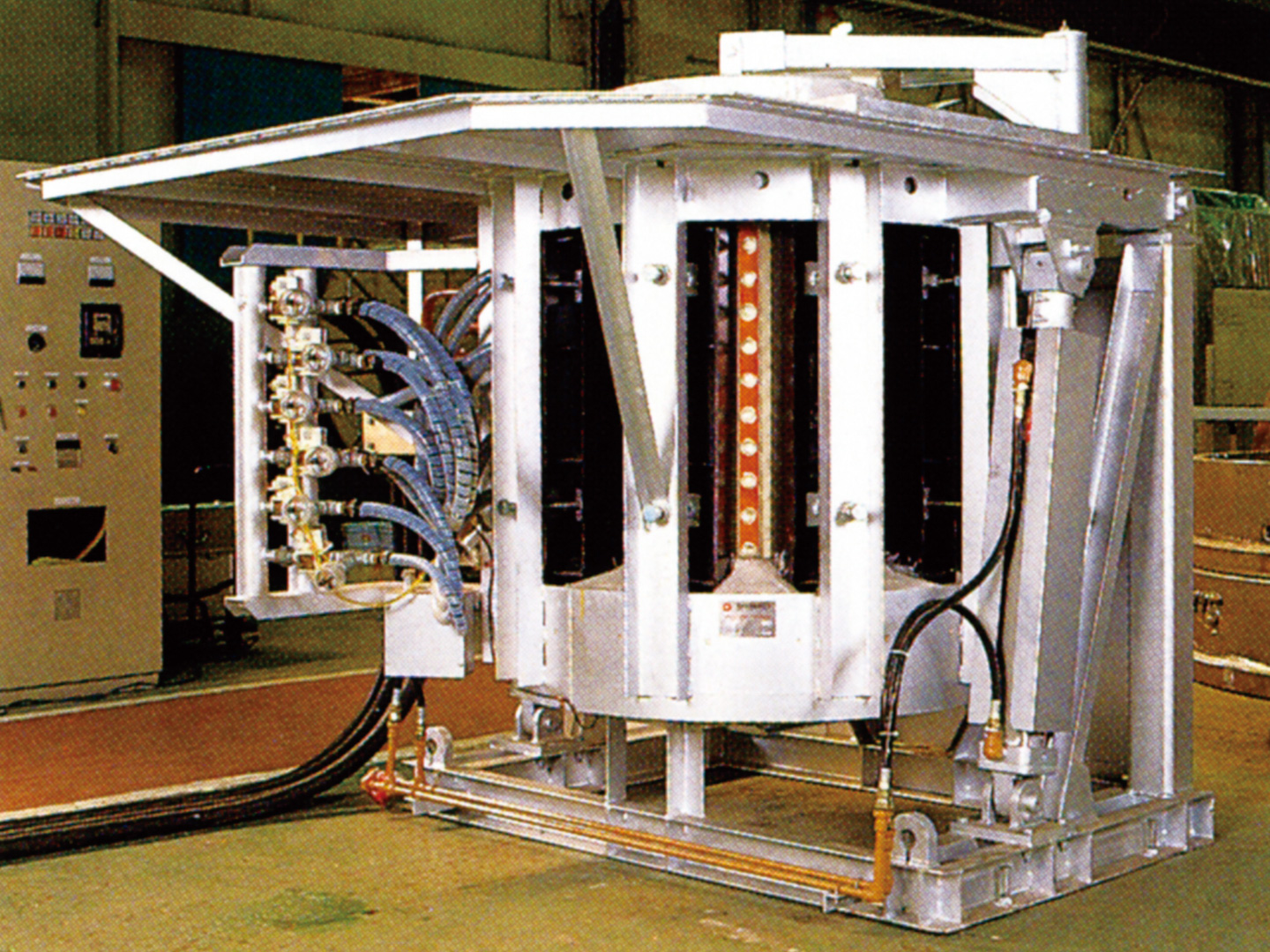
Efficient Furnace Body
- Minimizing magnetic reluctance by employing wide cross section area of yokes and L shaped yokes.
- Minimizing stray loss by employing the magnetic shield on top and bottom of the furnace body.
- Minimizing electrical loss with provision of by shortening the cable length via pulling out the water cooling cable from the side of furnace body.
Efficient Power Supply System
Employing sufficient Transistor inverter or Thyristor inverter.
Reliable Coil Insulation and Coil Protection
Employing thick inorganic insulation materials (Class H Mica for induction furnace) between coils for insulation.
Coating inside of the coil by a silicon rubber and covering all outside coil surface by insulations.

High Safety
Molten metal leak detection device works reliably when it occurs by special electrodes plastered in the coil cement.
Excellent Operation
Various patterns of operation and control via touch panel.
- Dissolution pattern setting (timer operation) such as starting from furnace cooling and sintering.
- Error and inspection guidance display.
- Demand control setting change.
- One touch electric power changing.
Easy Maintenance
Easy coil replacement because of the separated L shaped yokes enabling take-out of coil by itself.
Easy and fast replacement of the furnace linings by using the stamping lining machine and the extrusion type lining dismantling device.
High reliable metal leak detection device.
It uses a unique method to be plastered special electrodes between coil cements.
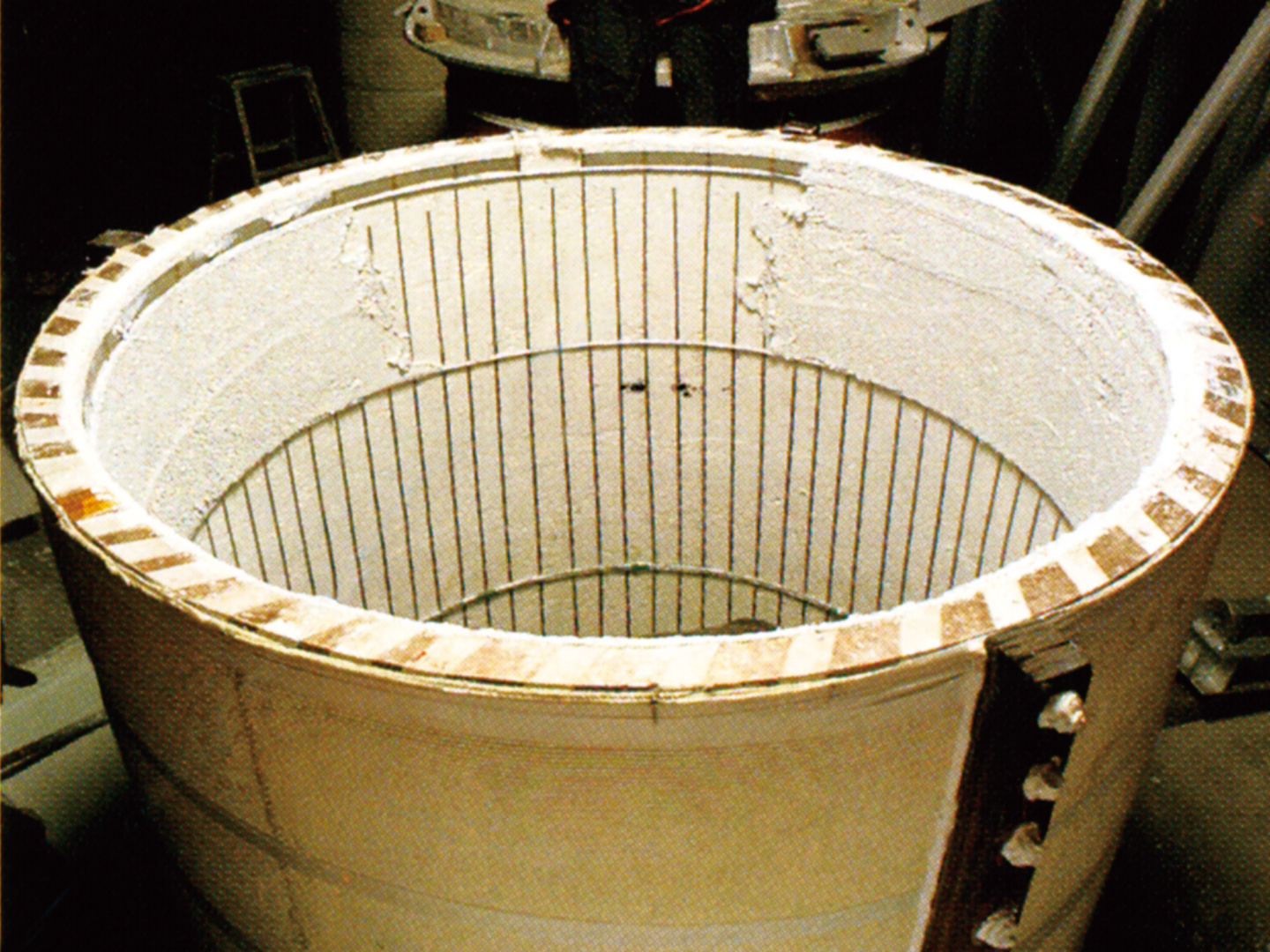
Water cooling cable drawn out from the side of furnace body.
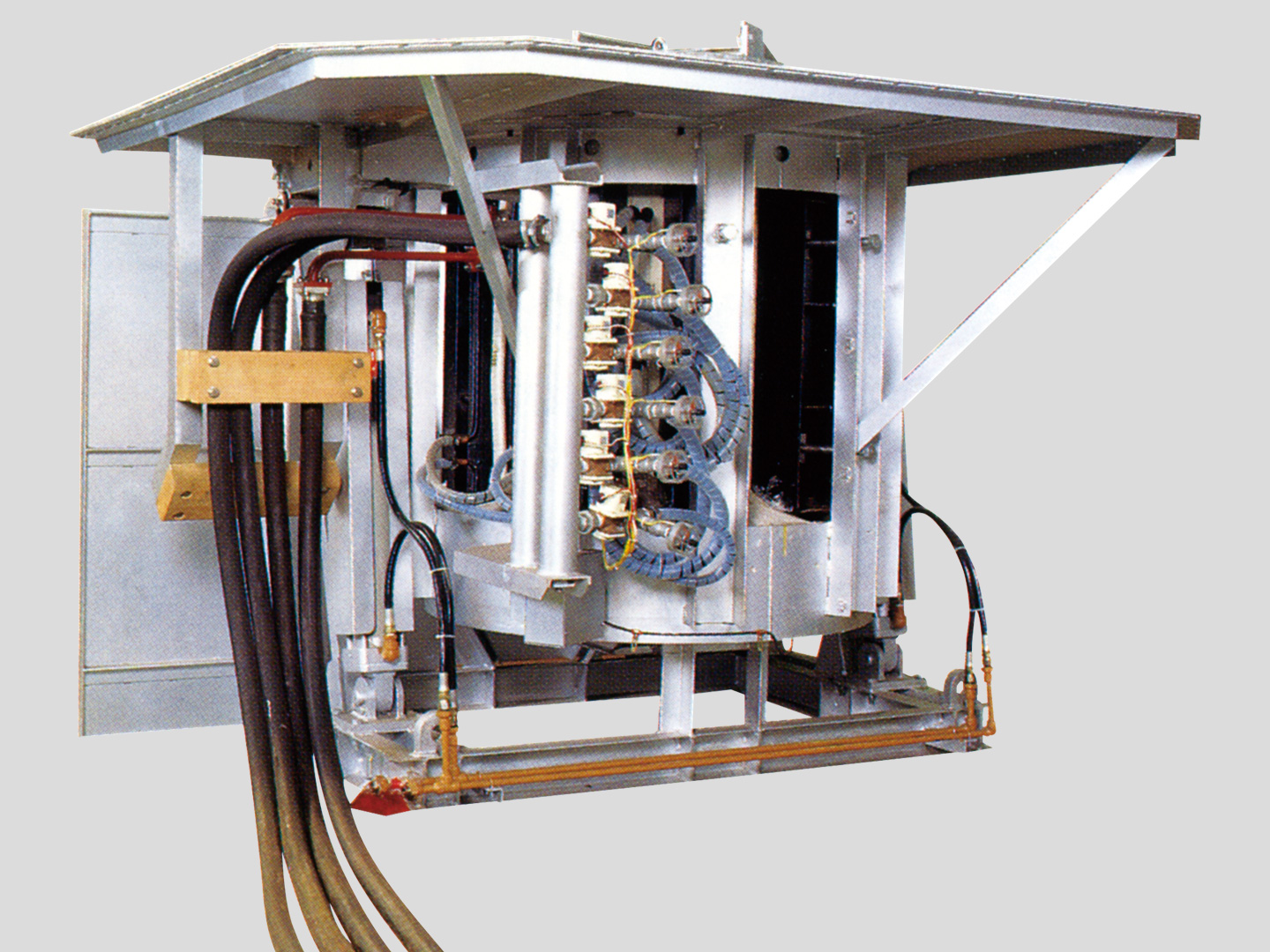
Device Configuration/Main Circuit Diagram
Device Configuration
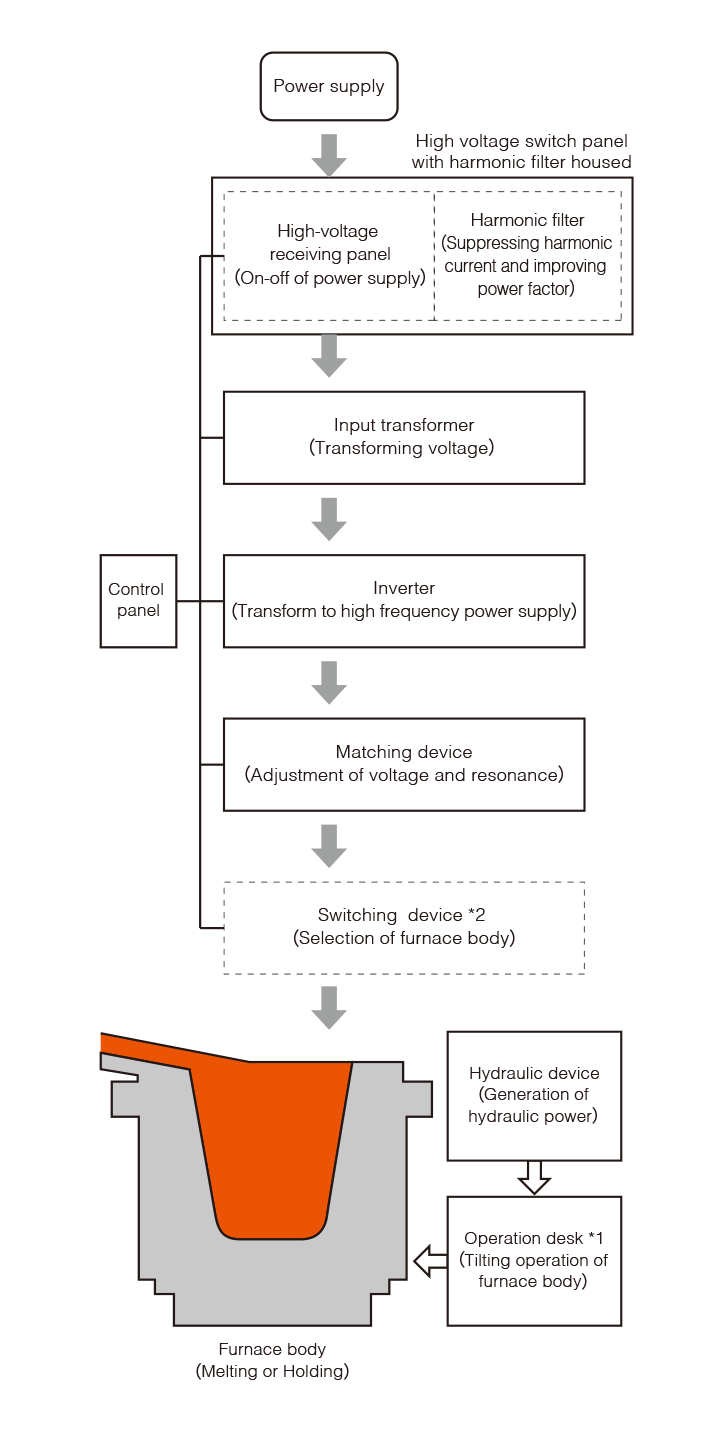
- Operation of open-close of the furnace cover by hydraulic pressure is optional.
- Switching device is unnecessary in case of 1power supply-1furnace body.
Main Circuit Diagram
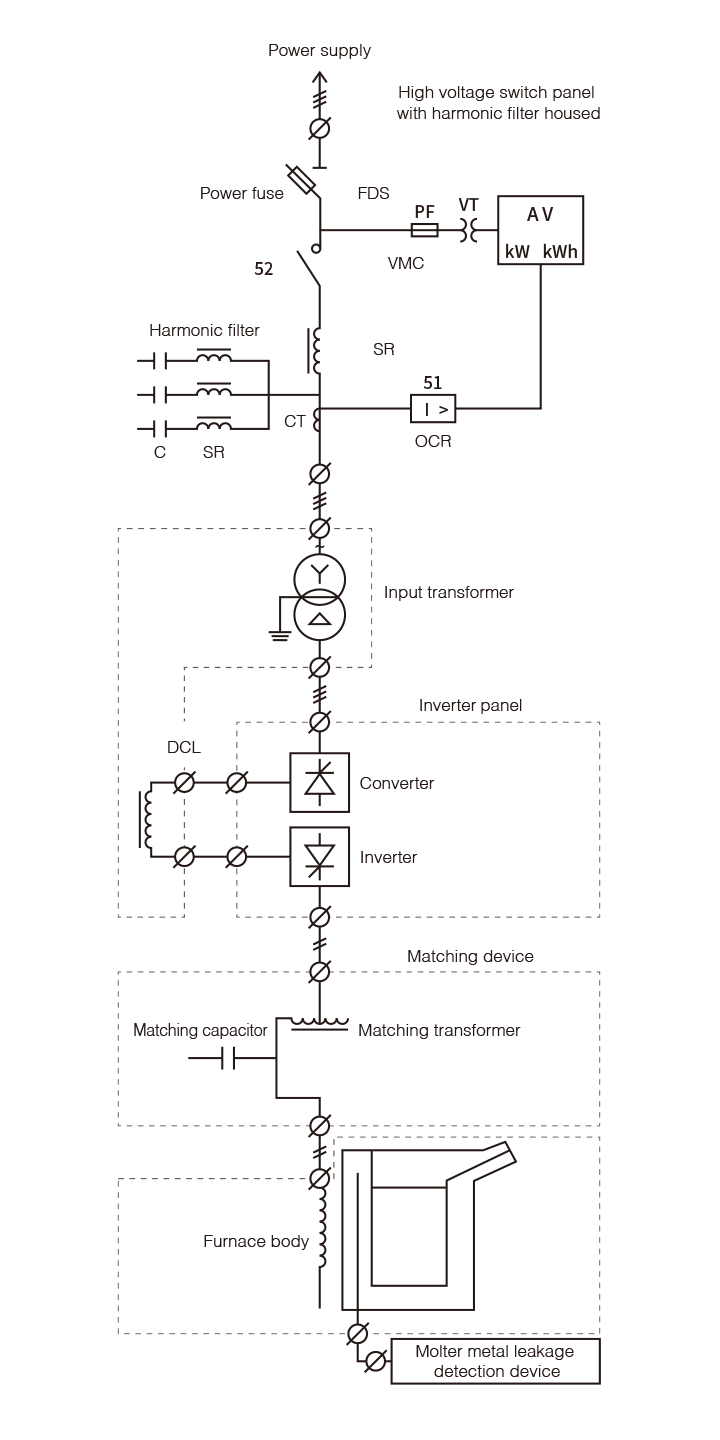
Cooling System
Water quality standard of cooling water for induction furnace, input transformer and capacitors.
Item | Reference range | Item | Reference range |
---|---|---|---|
Colored | Colorless | SiO2 | <20PPM |
Electric resistance | >3500Ω-cm | Evaporated residuum | <120PPM |
pH index | 6.5-7.5 | Chlorine ion (Cl-) | <30PPM |
total hardness | <100PPM | Sulfur ion (SO4-) | <20PPM |
All ion content | <0.5PPM | Ammonium ion | <0.1PPM |
Open enclosure type (standard)
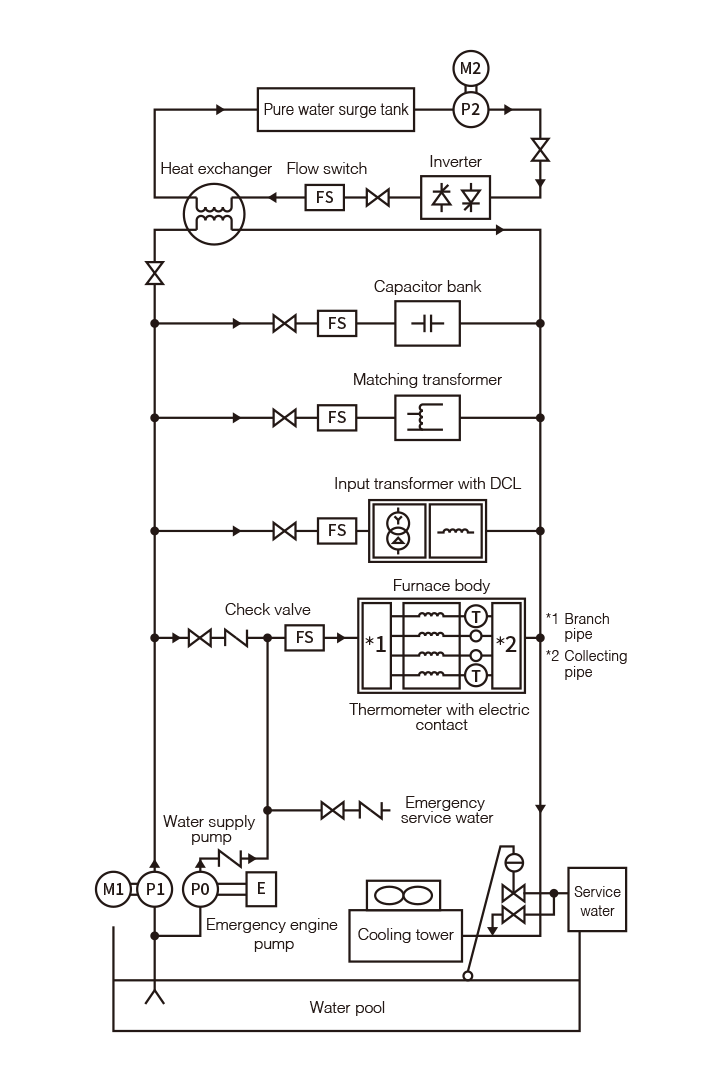
Closed enclosure type (option)
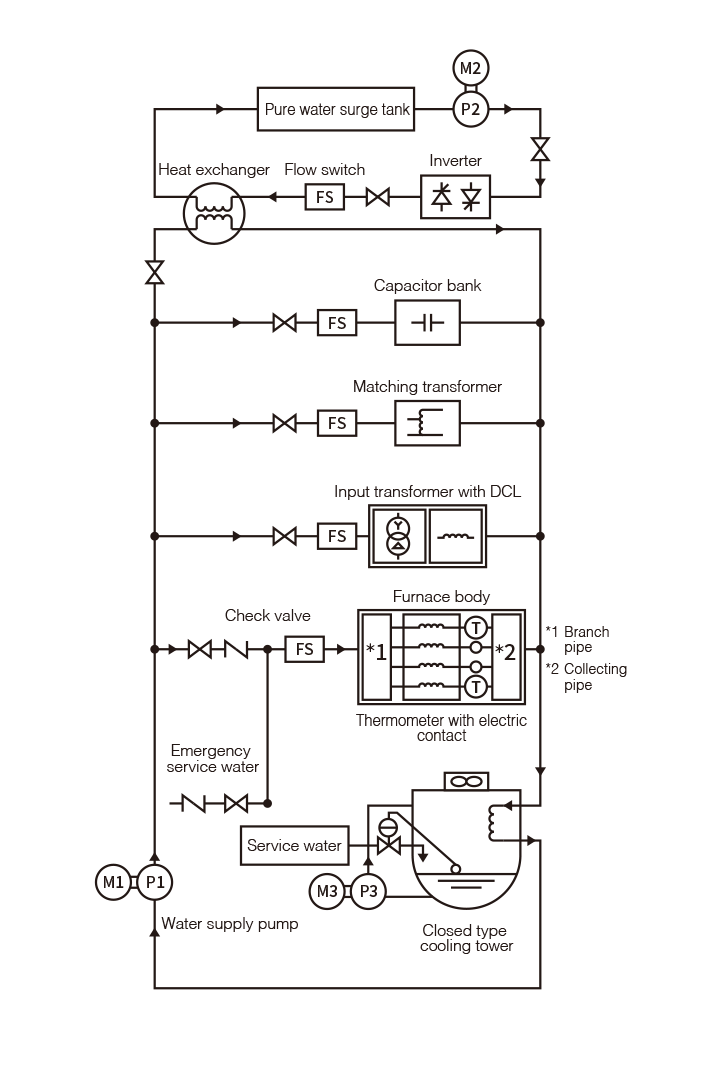
Characteristics
For melting cast iron and cast steel
Furnace type | Capacity (kg) |
Melting power (kW) |
Frequency (Hz) |
Cast iron 1500℃ | Cast steel 1600℃ | ||
---|---|---|---|---|---|---|---|
Power consumption (kWh/ton) |
Melting time (min) |
Power consumption (kWh/ton) |
Melting time (min) |
||||
HRS15A-30 | 15 | 30 | 3K | 790 | 24 | 860 | 26 |
HRS30A-50 | 30 | 50 | 2K | 760 | 28 | 790 | 29 |
HRS50A-100 | 50 | 100 | 2K | 690 | 21 | 760 | 23 |
HRS100MS-150 | 100 | 150 | 1K | 610 | 25 | 650 | 27 |
HRS200MS-200 | 200 | 200 | 1K | 585 | 36 | 645 | 39 |
HRS300MS-350 | 300 | 350 | 500.1K | 560 | 29 | 630 | 32 |
HRS500MS-350 | 500 | 350 | 500.1K | 570 | 49 | 620 | 55 |
HRS500MS-600 | 500 | 600 | 500.1K | 521 | 27 | 546 | 28 |
HRS1000MS-600 | 1000 | 600 | 500.1K | 524 | 53 | 560 | 58 |
HRS1000MS-900 | 1000 | 900 | 500 | 510 | 34 | 533 | 37 |
HRS1000MS-1200 | 1000 | 1200 | 500 | 500 | 25 | 521 | 28 |
HRS1500MS-900 | 1500 | 900 | 500 | 515 | 52 | 540 | 56 |
HRS1500MS-1200 | 1500 | 1200 | 500 | 505 | 38 | 531 | 41 |
HRS1500MS-1500 | 1500 | 1500 | 500 | 500 | 30 | 526 | 32 |
HRS2000MS-900 | 2000 | 900 | 500 | 523 | 70 | 543 | 76 |
HRS2000MS-1200 | 2000 | 1200 | 500 | 510 | 51 | 535 | 55 |
HRS2000MS-1500 | 2000 | 1500 | 500 | 503 | 41 | 528 | 43 |
HRS2000MS-1800 | 2000 | 1800 | 500 | 499 | 34 | 519 | 36 |
HRS3000MS-1200 | 3000 | 1200 | 500 | 512 | 79 | 537 | 83 |
HRS3000MS-1500 | 3000 | 1500 | 500 | 505 | 61 | 530 | 66 |
HRS3000MS-1800 | 3000 | 1800 | 500 | 500 | 51 | 525 | 54 |
HRS3000MS-2400 | 3000 | 2400 | 500 | 495 | 38 | 515 | 40 |
HRS5000MS-1800 | 5000 | 1800 | 500 | 502 | 86 | 527 | 91 |
HRS5000MS-2400 | 5000 | 2400 | 500 | 498 | 63 | 523 | 67 |
HRS5000MS-3000 | 5000 | 3000 | 500 | 497 | 50 | 511 | 53 |
HRS5000MS-3500 | 5000 | 3500 | 500 | 497 | 43 | 511 | 47 |
For melting copper alloy
Furnace type | Capacity (kg) |
Melting power (kW) |
Frequency (Hz) |
Copper alloy melting 1250℃ | |
---|---|---|---|---|---|
Power consumption (kWh/ton) |
Melting time (min) |
||||
HRC100MS-100 | 100 | 100 | 1000 | 399 | 25 |
HRC200MS-150 | 200 | 150 | 1000 | 381 | 31 |
HRC300MS-200 | 300 | 200 | 1000 | 374 | 35 |
HRC500MS-300 | 500 | 300 | 500 | 374 | 38 |
HRC1000MS-600 | 1000 | 600 | 500 | 346 | 36 |
- Melting time and power consumption on the above table are attained when the furnace is operated with hot lining suffi ciently and closed the cover without remaining molten metal in it. In any case, the time or electric power required for charging/discharging, slag-off, ingredient adjustment, temperature measurement, etc. are not included.
- Overcharge is allowed up to 10% of rating furnace capacity.
- Under the actual operation, the characteristics are variable depending upon operating conditions, such as materials and shape of melting materials, charging method and how to process molten metal, etc.
- Products having characteristics other than those indicated above are also available.
- n the above characteristics, there is a variation about 5% depending upon melting operation.
Outline Drawing
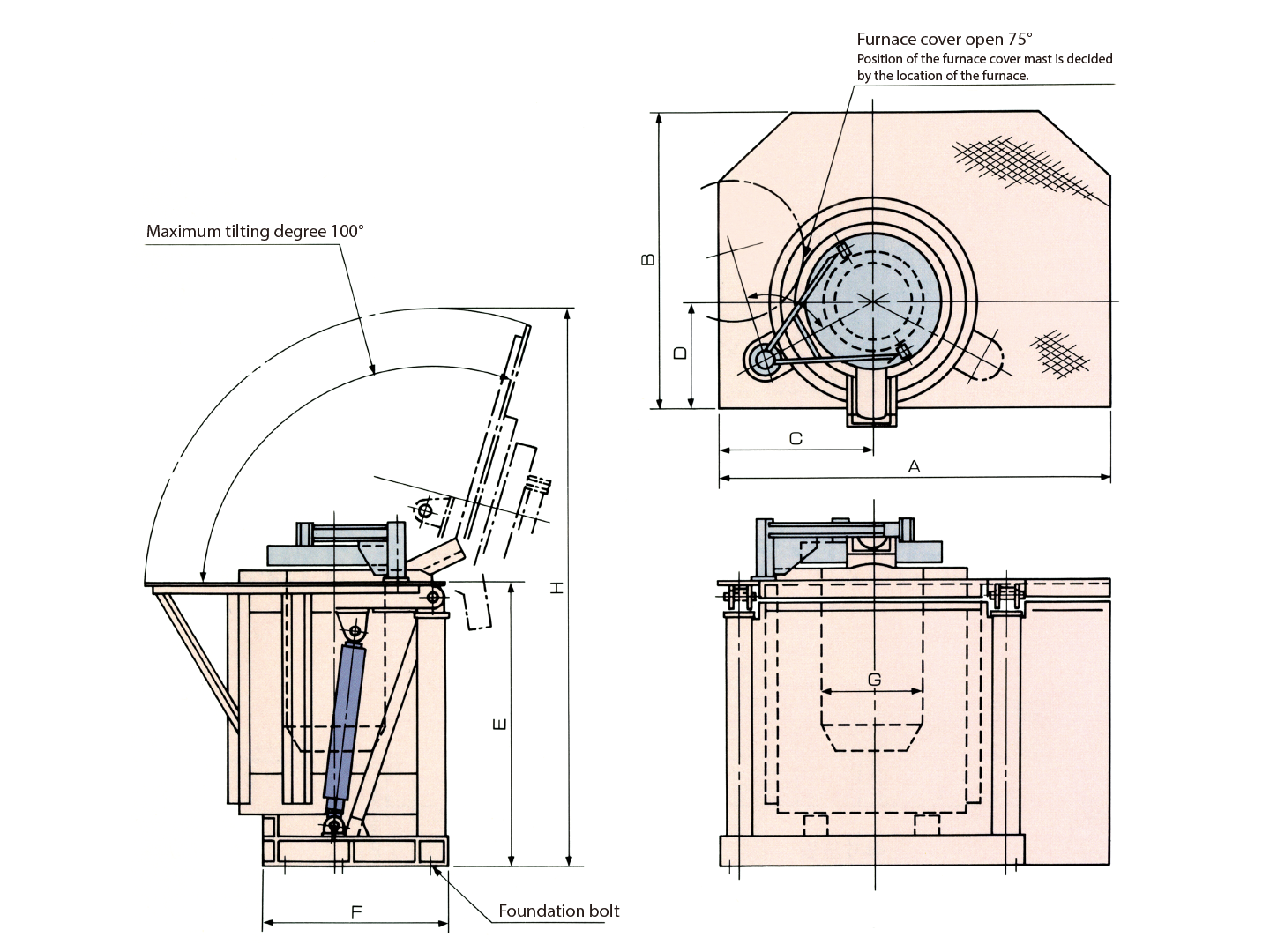
Dimensions table (Capacity indicates cast iron and cast steel)
unit:mm
Capacity (kg) |
Weight (kg) |
A | B | C | D | E | F | G | H |
---|---|---|---|---|---|---|---|---|---|
200 | 1750 | 1850 | 1530 | 700 | 480 | 1315 | 800 | 290 | 2780 |
300 | 2250 | 1950 | 1580 | 750 | 530 | 1405 | 870 | 330 | 2875 |
500 | 3300 | 2100 | 1745 | 825 | 595 | 1505 | 960 | 400 | 3130 |
1000 | 5350 | 2340 | 2090 | 925 | 690 | 1625 | 1105 | 500 | 3581 |
1500 | 6300 | 2500 | 2230 | 1000 | 730 | 1760 | 1200 | 600 | 3840 |
2000 | 7200 | 2650 | 2350 | 1050 | 750 | 1975 | 1250 | 630 | 4145 |
3000 | 10600 | 3100 | 2650 | 1175 | 850 | 2110 | 1380 | 720 | 4580 |
5000 | 13000 | 3700 | 3150 | 1400 | 1100 | 2550 | 1720 | 940 | 4828 |
Molten metal is not included.
After-sales Service Network
The induction furnace increases the possibility of sudden accident to every passing year, combined with being used in severe environments and doing insufficient services or maintenances in day-to-day. To prevent such troubles, it is essential to serve and maintain periodically. We have service centers across the world as the service company of Shinfonia Technology (formerly Shinko Electric Co., Ltd.), even if sudden equipment suspension occurs , we can provide safety and security in the on-call system.
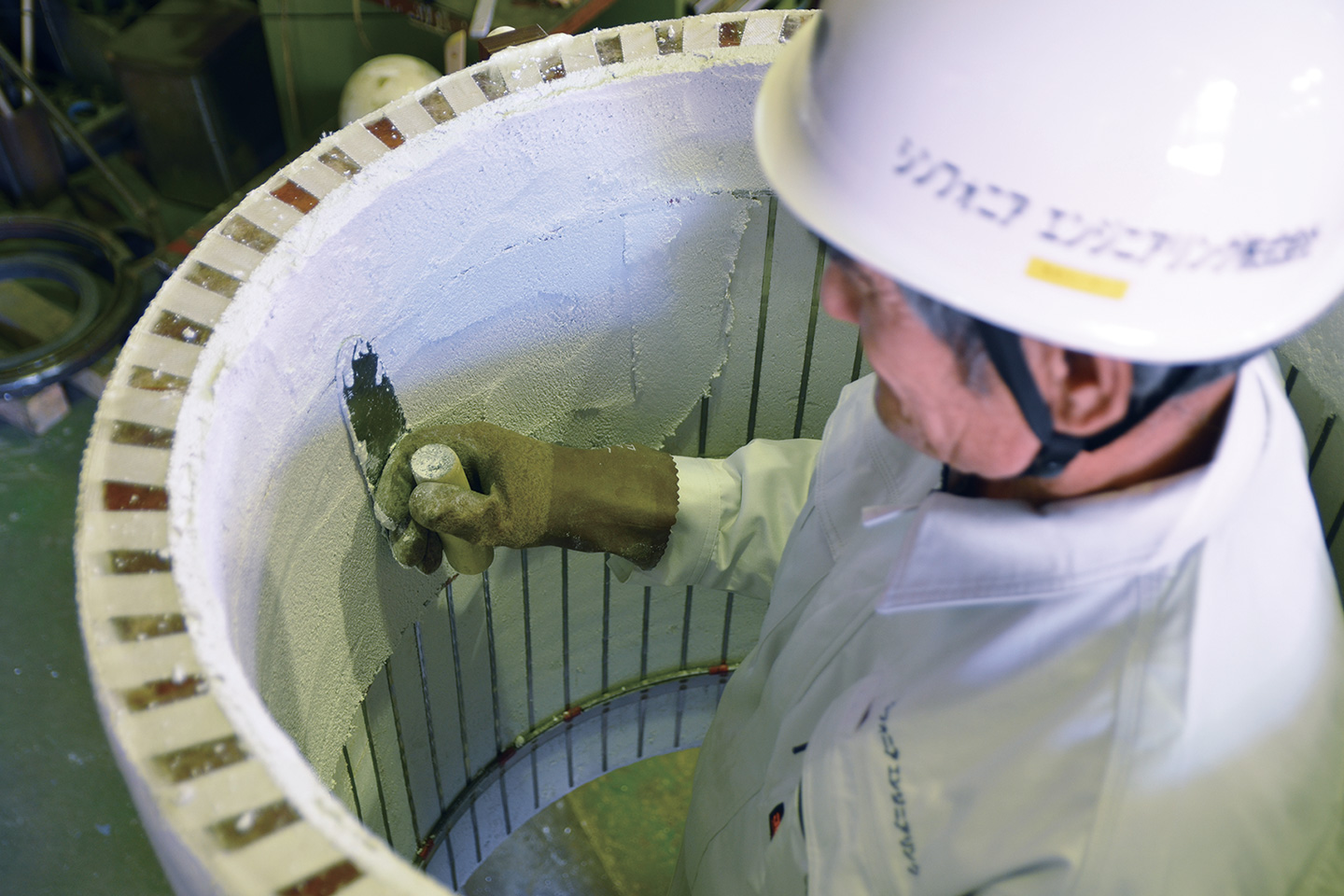